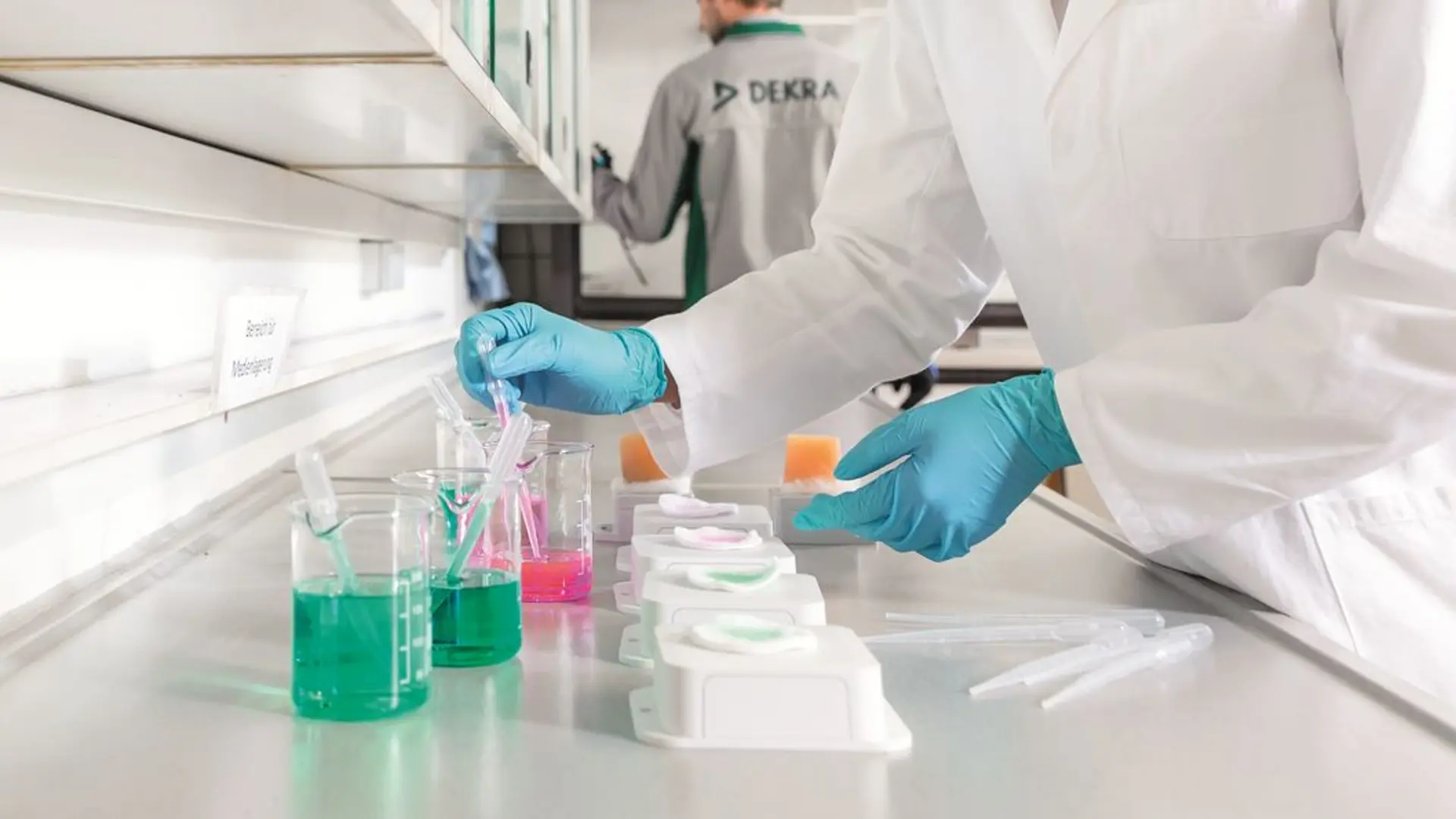
Laboratory sites DEKRA Automobil GmbH, Germany
Kontaktdaten
Handwerkstr. 17
70565 Stuttgart
Environmental simulation & surface resistance testing
Parts and components are exposed to various environmental stresses. With test chambers we simulate various climatic conditions in advance and use stress tests to check whether the function of a product is impaired. We assess surface properties and check surface coatings for their protective function against corrosion, UV radiation, mechanical stress and its media resistance.
Corrosion and salt spray testing for parts, packaging and license plates
Testing the corrosion resistance of components and technical products is an essential verification of the quality of materials and electroplated coatings. High resistance to corrosion must also be demonstrated for specific corrosion protection packaging and films, for example for metal and electronic products, as well as for licence plates, badges and adhesive seals.
With tests in the salt spray chamber, material testings can be carried out according to a wide range of national and international standards as well as customer specifications.
Your benefits from corrosion testing with DEKRA
- Large spectrum of test chambers for salt spray testing (CASS/NSS/AASS), cyclic corrosion tests and condensation water tests
- Wide range of corrosive conditions to test the durability of your products
- DIN CERTCO-approved test laboratory for retroreflective number plates DIN 74069
During their service life, components and coatings may be exposed to corrosive environmental conditions. Corrosion tests are intended to reproduce the corrosion process in nature in a short time. We simulate these corrosion conditions in advance. In doing so, we check whether the function of your products is impaired. Materials or components are exposed to a corrosive atmosphere in test chambers.
The test spectrum includes combined corrosion change tests. Changes in salt concentration, air humidity and temperature cause the corrosion environment on the material or component to change repeatedly. Condensation water tests are also used to clarify the behaviour and detect defects in the corrosion protection of the test specimens in humid environmental climates.
The DEKRA materials laboratory in Saarbrücken is also approved by DIN CERTCO as a testing laboratory for retroreflective number plates. After successful testing, you will receive the DIN testing and inspection mark.
Our corrosion testing services
- DIN EN ISO 9227 Salt spray test (NSS) in the test chamber
- AASS / CASS salt spray tests
- DIN EN ISO 11997 Resistance to cyclic corrosion conditions (cyclic corrosion test)
- DIN EN ISO 10289 Coatings and varnishes - corrosion testing of metallic and other inorganic coatings on metallic substrates
- VDA 621-415 Corrosion protection of vehicle paint by alternating cycles test
- Corrosion resistance test (intercrystalline corrosion)
- DIN EN ISO 6270-2 Resistance to humidity by condensation water test CH and AHT (former DIN 50017)
- Condensation water test climates (with / without SO2)
- DIN 74069 Retro-reflective registration plates, seal-sticker and sticker-cover for motor vehicles and trailers
- ISO 7591 Retro-reflective registration plates for motor vehicles and trailers